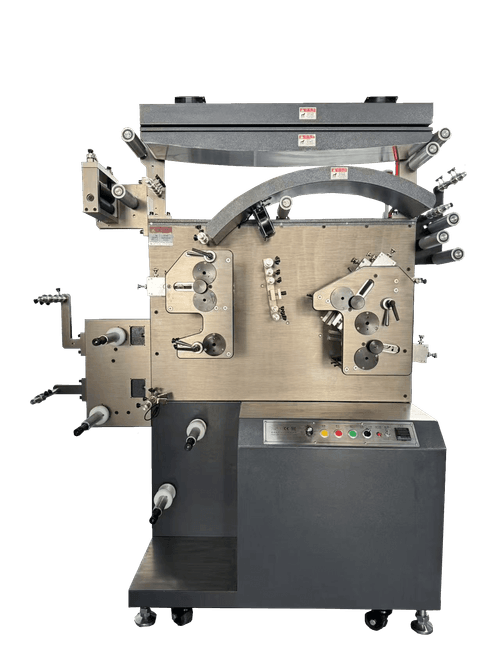
2025 Upgraded 2+1 Label Flexographic Printing Machine
Max Printing Area: 155mm(W)* 310mm(L)
Power: 220V/5KW
Max printing speed: 60m/min
Machine Dimension: 140cm(L)*72cm(W)*190cm(H๏ผ
Worry about the machine's quality and our service? We offer you 2 years long time warranty. Meanwhile, you can see what our clients say, click here.
๐ Why should you pick our Flexo Printing Machine for your label ribbon printing ๐
Our Flexo Label Printing Machine CY Series brings high-speed printing with fine, vivid colors and exquisite quality. It’s eco-friendly and perfect for printing all kinds of labels—polyester label tape, nylon tape, cotton label tape, herringbone tape, and roll paper. Washing-durable and colorfast, it’s a label printing solution you can count on. Here’s what makes it special:
- High-Precision Original Imported Machine Core Parts: Uses imported bearings from Japan for precise positioning, ensuring accurate color registration and reliability—peace of mind with a 2-year warranty. โ ๐ง
- Aluminum Alloy Machine Plate: Offers superior strength over competitors’ iron plates, resists corrosion, and keeps your Flexo printer looking brand-new for over 10 years. ๐ง๏ธ๐ซ๐ง ๐๐๐
- 100% Compatibility: Printing cylinders in metric or inch options, made with genuine materials for excellent value and a strong return on investment. ๐ฏ๐ฒ๐ฐ
- Over 20 Years of Industry Experience: With more than two decades in the game, our team’s expertise shines through. We focus on every tiny detail and prioritize top-quality service. ๐ฅ๐๐ ๐โจ ๐๐
- How It Works: Ink spreads evenly on anilox rollers, transfers to the printing cylinder, and the flexo photopolymer plate presses it onto your material. Change cylinder sizes for variable label lengths—easy!
- Machine Advantages:
- Tough aluminum alloy panel
- Japan bearings for precision
- Original imported silica gel heating plate
- Korean carbon fiber heating device
- Interchangeable anilox rollers and printing cylinders
- Variable frequency motor
- Matches parameters of UK Focus and CN Goldfai
1. Printing plate blank part of the roughened surface wear prone to failure
Over a long period, the roughened surface of the blank area may be worn away, resulting in:
(1) If the printing plate's water performance is reduced, you must increase the supply of Fountain Solution to maintain the ink balance.
(2) printing plate surface storage of water, adsorbed on the printing plate surface of less colloid, if printing short-term stop, do not rub glue is easy to get dirty, to the production of great inconvenience. Roughened surfaces wear more profound words. You must replace the printing plate.
2. Common Troubles and solutions in ink and wash painting
Problem 1: substrate bonding, rubbing dirty
Reasons for failure:
(1) The ink does not dry;
(2) rewinding tension is too large;
(3)Storage of printed materials at room temperature is too high
Solutions:
๏ผ1๏ผIncrease drying temperature;
๏ผ2๏ผReduce rewinding tension;
๏ผ3๏ผPrint the finished product in a cool place
Problem 2: The burnt version and the black version
FAILURE REASONS:
1. The printing plate is too shallow;
2. Printing pressure is too large;
3. Too much ink;
4. ink viscosity is too high;
5. INK DRYING RATE IS TOO fast;
Solutions:
1. Deepen Plate;
2. Adjust Printing Pressure;
3. Reduce Ink Supply;
4. Reduce INK viscosity;
5. Reduce the drying temperature
Problem 3: Poor color overlap
Reasons for failure:
1. Multicolor overprint the color behind before a color is not dry;
2. After the color makes a color-stripping phenomenon;
3. After the color overprint does not go up
Solutions:
1. Increase the drying speed of the first color;
2. Reduce the viscosity of the post-printing ink or Reduce Printing Pressure;
3. Reduce the viscosity of the post-printing or improve its adhesion
Problem 4:Printing pinholes
Reasons for failure: 1. Ink Roller drying too fast, uneven ink transfer;
Solution: 1. SLOW DOWN THE DRYING RATE OF INK;
Problem 5. Too Light
Reasons for failure:
1. Ink viscosity is too low;
2. The anilox Roller Line is too thin;
3 anilox Roller Worn or not clean; 4. Inking is too small
Rule Out methods:
1. Increase The viscosity of ink;
2. Replace the Coarse Line of the Roller;
3. Replace with a new roller or roller for thorough cleaning;
4. Reduce ink roller or knife pressure or appropriately increase the version of the roller pressure (gravure), and speed up printing (flexography).
Problem 6: It’s too dark
Reasons for failure:
1. Ink viscosity is too high;
2. anilox roller is too thick;
3. Ink Color Saturation is too high;
4. The Ink Volume is too large
Rule Out:
1. Add diluent to reduce viscosity;
2. Replace Fine Roller;
3. Add denaturant to reduce color depth
4. Increase ink roller or scraping knife pressure or appropriately reduce the pressure plate cylinder (gravure)
Problem 7. blotchiness in print
Reasons:
1. Plastic film of uneven thickness;
2. Ink is too thin;
3. Ink viscosity;
4. Printing plate ink is not uniform
Rule Out:
1. Replace the thickness of the uniform film;
2. ADD NEW INK;
3. Increase the stickiness of ink;
4. Check the cause of uneven ink transmission from ink and for ink